Flexible tubes are commonly used packaging materials for cosmetics. They are divided into round tubes, oval tubes, flat tubes, and super flat tubes in terms of technology. According to the product structure, they are divided into single-layer, double-layer, and five-layer flexible tubes. They are different in terms of pressure resistance, penetration resistance, and hand feel. For example, the five-layer tube consists of an outer layer, an inner layer, two adhesive layers, and a barrier layer.
一、 Basic appearance requirements
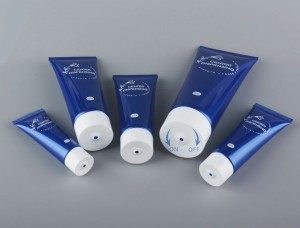
1. Appearance requirements: In principle, under natural light or 40W fluorescent lamp, visual inspection at a distance of about 30cm, there is no surface bump, embossing (no diagonal lines on the end of the seal), abrasions, scratches, and burns.
2. The surface is smooth, clean inside and outside, evenly polished, and the glossiness is consistent with the standard sample. There are no obvious unevenness, extra stripes, scratches or indentations, deformation, wrinkles and other abnormalities, no foreign matter adhesion, and no more than 5 small bumps on the whole hose. For hoses with a net content of ≥100ml, 2 spots are allowed; for hoses with a net content of <100ml, 1 spot is allowed.
3. The tube body and cover are flat, without burrs, damage, or screw thread defects. The tube body is tightly sealed, the end of the seal is flush, the seal width is consistent, and the standard size of the end of the seal is 3.5-4.5mm. The height deviation of the end of the seal of the same hose is ≤0.5mm.
4. Damage (any damage or rot at any position of the tube or cap); closed mouth; paint layer peeling off the hose surface> 5 square millimeters; cracked seal tail; broken head; serious thread deformation.
5. Hygiene: The inside and outside of the hose are clean, and there is obvious dirt, dust and foreign matter on the inside of the tube and cap. There is no dust, oil and other foreign matter, no odor, and it meets the hygiene requirements of cosmetic-grade packaging materials: that is, the total colony count is ≤ 10cfu, and Escherichia coli, Pseudomonas aeruginosa and Staphylococcus aureus must not be detected.
二、 Surface treatment and graphic printing requirements
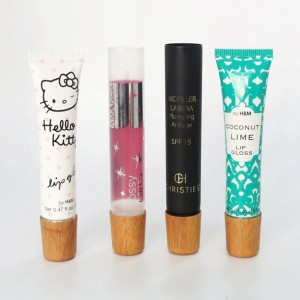
1. Printing:
The deviation of the overprint position is between the upper and lower limit positions confirmed by both parties (≤±0.1mm), and there is no ghosting.
The graphics are clear and complete, consistent with the sample color, and the color difference of the tube body and its printed graphics does not exceed the color difference range of the standard sample
The size and thickness of the text are similar to the standard sample, without broken characters, silted characters, and no white space, which does not affect recognition
The printed font has no obvious rough edges or ink edges, is correct, and has no wrong characters, missing characters, missing punctuation marks, missing text strokes, blur, etc.
2. Graphics:
The overprint is accurate, the overprint error of the main parts is ≤1mm, and the overprint error of the secondary parts is ≤2mm. No obvious heterochromatic spots and spots
For hoses with a net content of ≥100ml, 2 spots of no more than 0.5mm are allowed on the front, and the total area of a single spot does not exceed 0.2mm2, and 3 spots of no more than 0.5mm are allowed on the back, and the total area of a single spot does not exceed 0.2mm2;
For hoses with a net content of <100ml, 1 spot of no more than 0.5mm is allowed on the front, and the total area of a single spot does not exceed 0.2mm2, and 2 spots of no more than 0.5mm are allowed on the back, and the total area of a single spot does not exceed 0.2mm2. 3. Plate position deviation
For hoses with a net content of ≥100ml, the vertical deviation of the printing plate position shall not exceed ±1.5mm, and the horizontal deviation shall not exceed ±1.5mm;
For hoses with a net content of <100ml, the vertical deviation of the printing plate position shall not exceed ±1mm, and the horizontal deviation shall not exceed ±1mm.
4. Content requirements: consistent with the film and samples confirmed by both parties
5. Color difference: the printing and hot stamping colors are consistent with the samples confirmed by both parties, and the color deviation is between the upper and lower limit colors confirmed by both parties
三、 Hose size and structure requirements
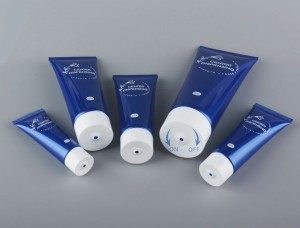
1. Specification size: measured with a vernier caliper according to the design drawings, and the tolerance is within the specified range of the drawings: the maximum allowable deviation of the diameter is 0.5mm; the maximum allowable deviation of the length is 1.5mm; the maximum allowable deviation of the thickness is 0.05mm;
2. Weight requirements: measured with a balance with an accuracy of 0.1g, the standard value and the allowable error are within the agreed range of both parties: the maximum allowable deviation is 10% of the standard sample weight;
3. Full mouth capacity: after filling the container with 20℃ water and leveling the container mouth, the full mouth capacity of the container is expressed by the mass of the water filled, and the standard value and the error range are within the agreed range of both parties: the maximum allowable deviation is 5% of the full mouth capacity of the standard sample ;
4. Thickness uniformity (suitable for hoses with contents of more than 50ML): Cut open the container and use a thickness gauge to measure 5 places at the top, middle and bottom respectively. The maximum allowable deviation is not more than 0.05mm
5. Material requirements: According to the materials specified in the contract signed by the supply and demand parties, refer to the corresponding national industry standards for inspection, and be consistent with the sealing sample
四、Tail sealing requirements
1. The tail sealing method and shape meet the contract requirements of both parties.
2. The height of the tail sealing part meets the contract requirements of both parties.
3. The tail sealing is centered, straight, and the left and right deviation is ≤1mm.
4. Tail sealing firmness:
Fill the specified volume of water and place it between the upper and lower plates. The cover should be moved out of the plate. In the middle of the upper pressure plate, pressurize to 10kg and keep it for 5 minutes. There is no bursting or leakage at the tail.
Use an air gun to apply 0.15Mpa air pressure to the hose for 3 seconds. No tail bursting.
五、Functional requirements of hoses
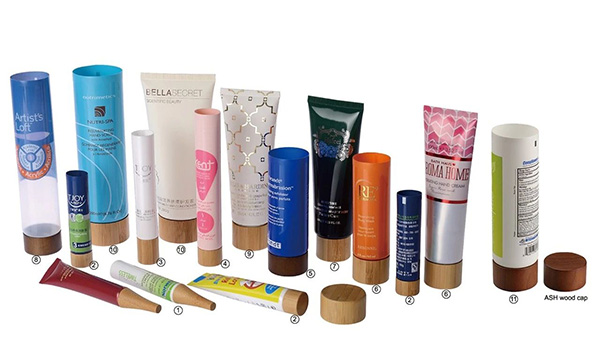
1. Pressure resistance: refer to the following two methods
After filling the hose with about 9/10 of the maximum capacity of water, cover it with the matching cover (if there is an inner plug, it needs to be equipped with an inner plug) and place it flat in a vacuum dryer to evacuate to -0.08MPa and keep it for 3 minutes without bursting or leakage.
Ten samples are randomly selected from each batch of materials; water of the same weight or volume as the net content of each product is added to the sample tube and placed horizontally naturally; the tube body is vertically statically pressed with the specified pressure for 1 minute, and the pressure head area is ≥1/2 of the container's force area.
Net content | Pressure | Qualified requirements |
≤20ml(g) | 10KG | No cracks in the tube or cap, no tail burst, no broken ends |
<20ml(g),<40ml(g) | 30KG | |
≥40ml(g) | 50KG |
2. Drop test: Fill the specified volume of contents, cover the lid, and drop it freely from a height of 120cm onto the cement floor. There should be no cracks, tail explosions, or leaks. There should be no loose fitting of the hose or lid, and no loose lid.
3. Cold and heat resistance (compatibility test):
Pour the contents into the hose or immerse the test piece in the contents, and place it in a temperature environment of 48℃ and -15℃ for 4 weeks. If there is no change in the hose or test piece and the contents, it is qualified.
Test one batch out of every 10 batches of materials; extract 3 covers from each cavity in a batch of materials, and the total number of covers that match the tube is not less than 20 sets; add water of the same weight or volume as the net content into the tube; heat 1/2 of the samples to 48±2℃ in a constant temperature box and place it for 48 hours; cool 1/2 of the samples to -5℃ to -15℃ in a refrigerator and place it for 48 hours; take out the samples and restore them to room temperature for appearance inspection. Qualification standard: There is no crack, deformation (appearance change that cannot be restored to its original state), or discoloration in any part of the tube or cover, and there is no cracking or breakage of the hose.
4. Yellowing test: Place the hose under ultraviolet light for 24 hours or in sunlight for 1 week. If there is no obvious discoloration compared with the standard sample, it is qualified.
5. Compatibility test: Pour the contents into the hose or soak the test piece in the contents, and place it at 48℃, -15℃ for 4 weeks. If there is no change in the hose or test piece and the contents, it is qualified.
6. Adhesion requirements:
● Pressure-sensitive tape peeling test: Use 3M 810 tape to adhere to the test part, and tear it off quickly after flattening (no bubbles are allowed). There is no obvious adhesion on the tape. Ink, hot stamping (the area of ink and hot stamping falling off is required to be less than 5% of the total surface area of the printed font) and large area of varnish (less than 10% of the total surface area) fall off to be qualified.
● Influence of contents: Rub back and forth 20 times with a finger dipped in the contents. The contents do not change color and no ink falls off to be qualified.
● The hot stamping shall not have a diameter of more than 0.2mm falling off, no broken lines or broken characters, and the hot stamping position shall not deviate by more than 0.5mm.
● Silk screen printing, hose surface, hot stamping: One batch is tested for every 10 batches, 10 samples are randomly selected from each batch of materials, and soaked in 70% alcohol for 30 minutes. There is no falling off on the hose surface, and the unqualified rate is ≤1/10.
六、Requirements for fit
1. Tightness of fit
● Torque test (applicable to thread fit): When the threaded cap is tightened at the hose mouth with a torque of 10kgf/cm, the hose and cap are not damaged and the threads do not slip.
● Opening force (applicable to the fit of the hose with the cap): The opening force is moderate
2. After fitting, the hose and cap are not skewed.
3. After the hose cap is fitted, the gap is uniform and there is no obstruction when touching the gap with your hand. The maximum gap is within the range confirmed by both parties (≤0.2mm).
4. Sealing test:
● After filling the hose with about 9/10 of the maximum capacity of water, cover the matching cap (if there is an inner plug, the inner plug must be matched) and place it flat in a vacuum dryer to evacuate to -0.06MPa and keep it for 5 minutes without leakage;
● Fill water according to the net content specified in the container, tighten the cap and place it flat at 40 ℃ for 24 hours, no leakage;
Post time: Jun-05-2024